鍛造ソリューション
鋳造部品の鍛造化
鋳造部品の鍛造化
鋳造部品の鍛造化を図る事で、不良率を大幅に改善。
継続発注により、コスト削減も可能な理由を解説
近年、鋳造加工メーカーの減少に伴い、「部品の製造工法を鍛造へ切換えたい」と、ご相談頂く事例が増えています。このようなニーズに対し、中野鍛造所では、鍛造化による製品強度の向上と安定した部品精度や品質の改善を実現しています。さらに、コスト面においても、継続発注によって結果的にコスト削減が可能になる理由について解説いたします。
鋳造部品から鍛造部品への変更で、強度と品質の両方を同時に向上させることが出来ます
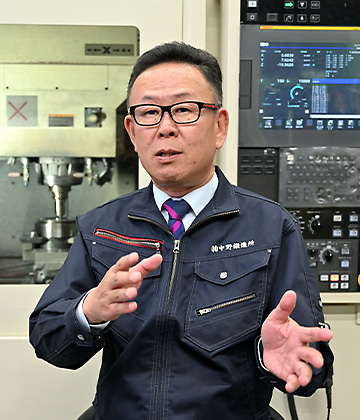
德田 勝也
従来、鋳造により製造していた部品を、鍛造に切換えるケースが増えているのは何故でしょうか?
鋳造は、複雑形状の成型に適しており、製造コストも鍛造に比べて比較的安価であることから、金属部品を製造する際の選択肢の一つとなっています。
その一方で、鋳造は気温や湿度の影響を受けやすく、技術者の技能に製品品質が左右されます。また、鋳造特有の「巣」と呼ばれる、気泡による内部欠陥が発生し、不良率も5~10%程度発生する事をあらかじめ織り込んでおく必要があるなど、どうしても品質面で不安定要素があることは否めません。
その様な中、近年、ますます鋳造技術者の高齢化が進んでおり、後継者不足により廃業されるケースも多く見受けられるようになりました。それらの対策として、発注担当者様は、部品の安定供給元を確保する為、鋳造から鍛造への工法転換を検討されている側面もあります。
実際、私共にも、そうしたお客様から多数のお問い合せを頂き、鋳造部品の鍛造化にご対応させて頂いているところです。
中野鍛造所へ鍛造化を依頼したお客様は、どのような成果を得られていますか。
強度については、鋳造品を鍛造化する事により金属組織が緻密になり、確実にアップいたします。
また、品質においても、鋳造で発生していた内部欠陥の気泡である「巣」の問題も解消され、製品の面粗度も良好になるなど、向上を実現できます。さらに、中野鍛造所では、業界トップクラスの不良率0.00001%を達成しているため、品質面では相当に自信を持っております。
実際、中野鍛造所へ鍛造化をご依頼頂いたお客様から、
「明らかに、強度・品質が向上した」
「従来は歩留まりが悪く、納期ズレするリスクがあったが、高品質な製品が納期通りに入手できるようになった」
という嬉しいお声を頂いております。
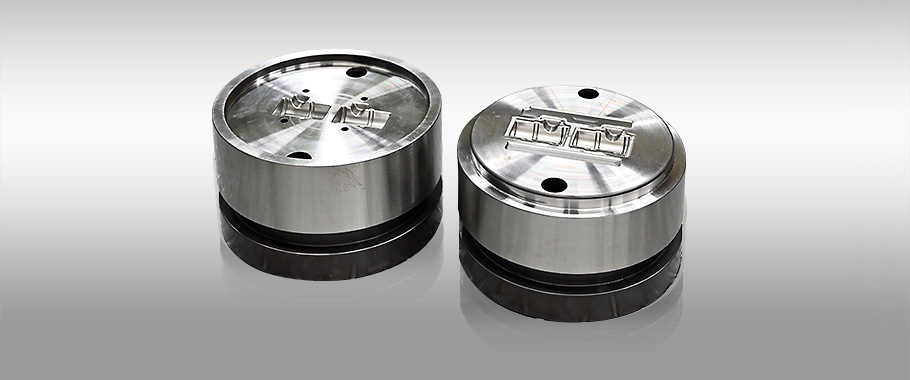
(2個取りによるコスト削減例)
鍛造の場合、継続発注によって金型代金回収し、
コスト削減効果を得て頂く事が可能です
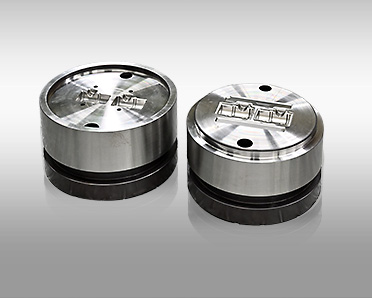
(2個取りによるコスト削減例)
鍛造の場合、金型が必要となるため、鋳造よりコストがかかるイメージがありますが、実際はどうでしょう?
おっしゃる通り、鋳造から鍛造化へ工法転換する場合、概ね通常10~30%のコストアップとなります。また、鋳造においては安価な砂型を使用しますが、鍛造では専用の金型を用いるため、その分の初期費用が必要となります。
しかし、その金型代は、今後継続して発注される場合、製品1個単位の費用が安くなるため、最終的に回収する事が可能となります。不良率の高い鋳造よりも、トータルな製造支出コストを見て頂く事で、収益的にプラスが出て来ている企業様が多くいらっしゃいます。
つまり、まとまった数量の製造が見込まれる部品であれば、今すぐ鍛造に変えた方がお得になると言えます。
さらに中野鍛造所なら、薄肉化(材料減)や部品の一体化等
再設計を図る事でコスト削減を実現しています
鍛造化を図られるお客様にメリットを出せる、中野鍛造所ならではの技術は何でしょうか?
当社では、鋳造品の鍛造化をお考えのお客様に、併せて製品形状の再設計を御提案しています。
殆どの場合、鋳造製品の形状をそのまま鍛造成型することは難しく、鍛造に適した形状に再設計する事が必要になります。
中野鍛造所では、お客様から現行製品のサンプルと図面をお預かりし、課題分析を行います。そして、鍛造工法を選ばれた場合、材料費削減のための薄肉化や、補強が必要な箇所への増肉、金型から製品を抜き出すために必要な「抜き勾配」といった形状変更を、お客様のご了解の下に行っています。取付箇所によっては、鍛造による複数部品の一体化も実現可能です。
当社の強みは、鍛造のみならず、鍛造金型の設計・製造も社内で行っている事です。実は、熱間鍛造業界では、社内で金型設計・製造を行っている加工メーカーは僅かで、殆どが外注で行っています。そのため、実際に初回鍛造を行った後で、「少し長さを伸ばしてほしい」「少し径を太くしてほしい」といった小変更へのご要望にも、スピーディーに対応できている事は、お客様への大きなメリットとなると考えています。
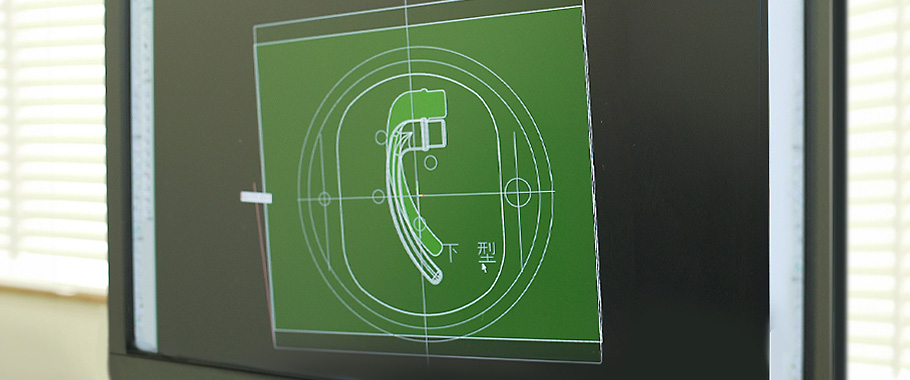
熱間鍛造金型の設計
鋳造からの鍛造化により、検査等の工程が削減。
トラブルフリーとなり高効率化が図れます
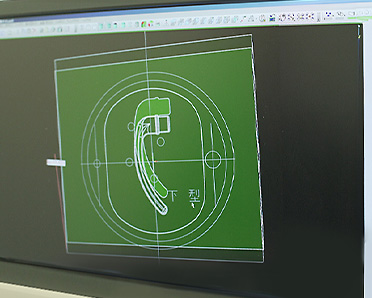
熱間鍛造金型の設計
鍛造化によって、組立工程の他、検査工程の削減も可能になりますか?
はい。例えば、流体を扱うバルブ製品において、鍛造化を行う事で圧力検査を不要にした実績例がございます。こちらのバルブは、従来、鋳造された2個の部品を溶接で組立てて製品を完成させていましたが、溶接部の品質にバラツキが継続してた為、圧力検査を全数に対して行い、流体漏れの有無をチェックしていました。
このバルブの鍛造化に当たり、中野鍛造所では再設計を行い、2個の部品の一体化成形を実施させて頂きました。この工法ですと、そもそも漏れの原因となる継目がないためトラブルフリーにあり、簡単なサンプル検査を行うだけで十分な品質を担保することが可能になりました。
その他、お客様が得られるメリットを教えてください。
鋳造の場合、ロットによってパーティングライン(型と型の合わせ面に発生する凸部)の位置が変化するため、切削加工の際に、チャッキング(マシンへの取付)に手間取るケースがありました。
鍛造化することにより、パーティングラインの位置は常に一定となりますので、切削工程でのチャッキングが容易で、作業効率が向上します。このように、中野鍛造所に一貫してお任せ頂く事で、管理の手間を省くことが可能になり、トータルコストの削減が図れるなど、大きなメリットを得て頂く事が可能です。
鋳造部品の鍛造化について、
万全のサポートでお応えします
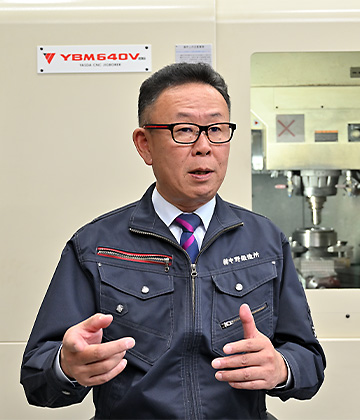
最後に、鋳造部品の鍛造化を検討中の担当者様へ、メッセージをお願いします。
中野鍛造所では、鋳造部品の鍛造化を検討されている担当者様に、最適なアドバイスをさせて頂いております。
例えば、鍛造化によるコストアップをできるだけ抑えるための薄肉化や、複数部品の一体化など、「トータルコスト削減」に繋がる様々なソリューションを御提案いたします。
鋳造から鍛造への工法転換をお考えのお客様は、是非一度中野鍛造所までご相談ください。万全のサポートでお応えさせて頂きます。
鍛造ソリューション